Helping enterprises know the unknown.
Previously, we talked about Willowmore's quality control assurance before any order fulfilment. This week, we want to discuss about the potential Return On Investment (ROI) that businesses could gain simply by switching their current key-lock system to an enterprise keyless smart lock system.
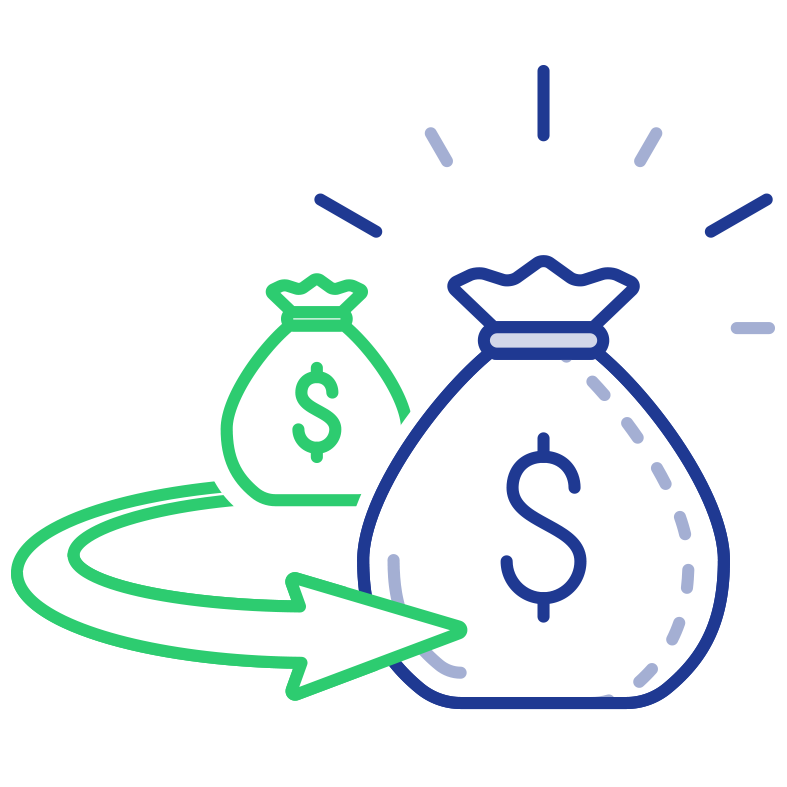
Quantifiable benefits:
On the first post, “The birth of a industrial smart access control management system” , we highlighted that the current process of managing a physical key-lock system is time and cost consuming. There is also an absence of visibility for operators to monitor or control access to sites. Most telecom sites are secured by mechanical locks, which means that the keys must be stored at a secure and easy-to-reach place. However, evidence suggests this is usually not the case. Anyone that visits a remote site must first collect the key from the central office. This commute could take up to 5-6 hours and consume at least 5-8 litres of fuel (per visit) due to unforeseen traffic conditions. In addition, keys are often duplicated or misplaced which expose telco sites to vandalism and theft. Some operators have reported that they use combination locks or store keys somewhere nearby the remote sites, resulting in managers at the monitoring centre having zero visibility on who is accessing the site, for what purpose and for how long.
Let us give you an example: An operator has 15,000 sites, 10 preventive and 4 corrective maintenance programs are conducted on each site yearly. Based on our case studies, a technician takes approximately 4 hours to travel to pick up and drop off keys. Willowmore’s solution cuts down 840,000 hours of traveling time, saves USD5,040,000 in manpower costs and eliminates USD243,600 in fuel expense. The total savings can go up to USD5,283,600.
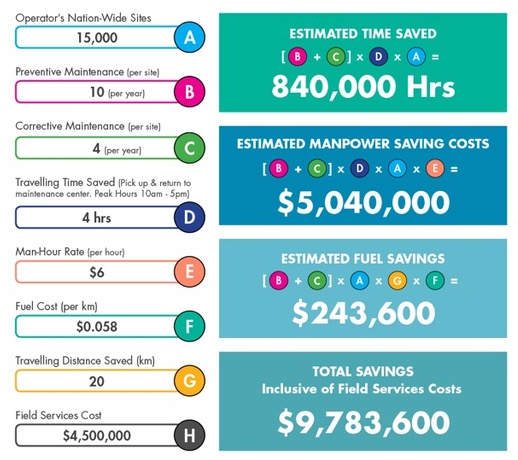
Unquantifiable benefits: Prevention is better than cure.
We estimated that operators can save up to 30% of field services costs. Operators typically pay USD1000/site per annum, not knowing if contractors actually show up to get the jobs done or how long they spend on site. With our data, operators can track visitors, their tasks and time spent on site. Willowmore provides a powerful tool for operators to choose the most efficient contractors based on productivity and at the same time, stop paying for no-show jobs.
In perspective, we help operators save up to USD4,500,000 a year on field services costs. This is not inclusive of the amount that we help operators save due to lower thefts in batteries, copper equipments and the intangible benefit of bringing a site back faster. Operators can look to saving more than USD9,000,000*/annum by simply swapping their mechanical lock system to our smart locks.
As one of our customers mentioned: "We don’t know the unknown". Therefore, it is Willowmore's mission to let you "Know the unknown".
*On average, engineers only took 1hr travelling to and from maintenance centers. Amount of fuel saved is averaged based on multiple factors (peak/non-peak hours and traffic jams). Rates and figures are correct during date of trial. The information provided in this document is intended for informational purposes only and is subject to change without notice.